Любая организация, которая поддерживает систему качества, сталкивается с необходимостью создания эффективной системы работы с корректирующими и (или) предупреждающими действиями (далее, САРА).
В данной заметке представлен подход, принятый на многих предприятиях автомобильной промышленности – т.н. методика 8D. Каждый шаг методики 8D имеет в своем наименовании букву «D», что означает «discipline» – по сути, применение мер регулирования, приведение к некому порядку, упорядочивание и т.п.
Методика 8D является одним из универсальных процессов устранения проблем качества. В автомобильной промышленности данная методика считается достаточно эффективной. Именно такой алгоритм работы с САРА принят у мировых гигантов General Motors, Ford Motors, Daimler Chrysler, Honda и др.
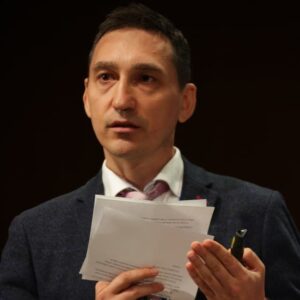
В автомобильной промышленности данная методика считается эффективным инструментом определения и устранения коренных причин проблем качества. Например, Ford Motors Company требует от своих поставщиков применения методики устранения проблем качества G8D (Global Eight Discipline), General Motors – PR&S (Problem Response & Solutions), Daimler Motors – 7 Steps, Honda – 5P и т.п. – все это элементы методики 8D.
У методики 8D много преимуществ. Одно из них – проведение тщательного исследования системы (процесса, объекта), в которой возникла проблема качества и предотвращение ее повторного возникновения в будущем. По своей сути методика 8D близка к FMEA, с той лишь разницей, что FMEA применяется для предотвращения отказов, несоответствий и других проблем качества, а 8D после реализации данных событий. Еще одним достоинством считается легкая интеграция с проектами Six Sigma, особенно в вопросах коммуникации и получения данных о проблемах качества от поставщиков.
Что такое 8D
Методика 8D – это упорядоченный (дисциплинированный) процесс устранения проблемы качества методологическим и аналитическим путем, разделенный на 8 этапов:
- D0 – Подготовка.
- D1 – Формирование команды.
- D2 – Описание проблемы.
- D3 – Определение временных мер.
- D4 – Поиск коренной причины (расследование).
- D5 – Подбор и верификация корректирующих действий для коренной причины и определение т.н. точки потери контроля.
- D6 – Реализация и оценка достаточности корректирующих действий.
- D7 – Выбор предупреждающих действий.
- D8 – Закрытие проблемы.
Каждый из этапов методики имеет свои входные и выходные информационные потоки.
D0 – Подготовка
Основная задача этого этапа – определить значимость проблемы и необходимость реализации оперативных (экстренных) действий, т.н. emergency response action (ERA), направленных на изолирование проблемы и (или) минимизацию последствий ее реализации.
Примеры оперативных (экстренных) действий – сортировка продукции, перемещение продукции в карантин, (при)остановка операционной деятельности (производства, отгрузки, и др.), отзыв продукции и т.п.
D1 – Формирование команды
Как правило, команда для 8D формируется из специалистов разных структурных подразделений, в зависимости от характера выявленной проблемы качества с учетом имеющихся компетенций и опыта специалистов. Вопрос очень индивидуальный, но есть несколько советов:
- Лучше формировать команду не более 3-5 человек, иначе проблема не решится, будет решаться не в том направлении или не так как хотелось бы.
- Члены команды должны иметь полное представление и знание объекта оценки (продукции, процесса, системы).
- Члены команды должны знать методологию устранения проблем и управления САРА.
- В команду необходимо включать только тех, у кого есть желание выполнять такую работу и имеющие временной ресурс.
- Членам команды должна оказываться поддержка со стороны высшего руководства.
Входом для D1 является решение использовать методику 8D для устранения проблемы из D0. Выходом – сформированная команда для выполнения последующих этапов с установленной ответственностью (ролями) участников.
Данный этап может быть оформлен в виде таблицы с указанием:
- ФИО участника команды.
- Структурного, подразделения, которое представляет участник.
- Имеющегося у него опыта (чем может быть полезен?).
- Зона ответственности (роль), например: лидер команды; ответственный за сбор и анализ данных по производственному процессу; ответственный за сбор и анализ данных по поставщикам; оценка работы персонала и т.п.).
D2 – Описание проблемы
Пожалуй, самая основная и важная часть всего процесса. На данном этапе необходимо понять и описать возникшую проблему качества и ее симптомы. От того, насколько правильно будет описана проблема, в дальнейшем будет зависеть правильность определения коренной причины и эффективность корректирующих действий.
Члены команды должны понимать, что необходимо найти и устранить именно коренную причину, а не ее симптомы.
Описание проблемы обычно содержит три части:
- Объект (это продукция, изделие, компонент или ситуация).
- Предмет проблемы – сама проблема (дефект, отклонение, несоответствие, нарушение).
- Радиус зоны бедствия – нанесенный ущерб, тяжесть последствий, количество дефектных изделий и т.п.
Для описания проблемы могут применяться самые разные техники, начиная от «причинно-следственной диаграммы» (Исикава), «пяти почему», метода «Is-Is Not» и заканчивая сложными алгоритмами вероятностных расчетов. Каждый раз нужно подобрать именно ту технику, которая может вывести на коренную причину проблемы качества.
D3 – Определение временных мер
На данном этапе определяется набор действий, требуемых для уверенности в том, что последствия проблемы изолированы и ситуация взята под контроль. Например:
- До завершения производственной кампании обеспечить проведение дополнительного контроля конкретного параметра (или показателя качества) не реже 2 раз в смену.
- Провести калибровку средства измерений.
- Провести сортировку или переработку продукции
и т.п.
На данном этапе может потребоваться получение дополнительных разрешений (санкций) на временные меры (например, от Отдела контроля качества, Отдела обеспечения качества, Службы охраны труда и т.п.).
D4 – Поиск коренной причины (расследование)
На данном этапе 8D команда проводит исследование и анализ коренной причины. Вполне вероятно, что это будет не одна причина, а целый каскад первоисточников проблемы. Основная задача – понять, каким образом проблема не была выявлена (обнаружена) на стадии оценки проектного решения, разработки, производства, контроля, отгрузки и т.п. Главное правило на данном этапе – только «Почему?» и никогда «Кто?».
Типовые вопросы:
- Была ли замена (изменение) узлов оборудования или ремонт?
- Была ли замена поставщика сырья и (или) материалов?
- Вносились ли какие-либо изменения в производственный процесс или связанную с ним стратегию контроля?
и т.п.
Если команда считает, что причина проблемы качества уже установлена на этапе D2 и имеются данные о валидации, подтверждающие (доказывающие) правильность суждений – тогда можно сразу переходить к escapepointна этапе D5.
D5 – Подбор и верификация корректирующих действий для коренной причины и определение т.н. escapepoint
Данный этап предусматривает подбор корректирующих действий и определение т.н. escape point. По определению escape point (ЕР) – это наиболее близкая точка в процессе, где проблема качества должна была быть или могла быть обнаружена, но не была обнаружена (точка потери контроля). Идентификация данной точки позволит пересмотреть стратегию контроля, внести необходимые дополнения или изменения в рабочие инструкции, стандартные операционные процедуры, проверочные листы (чек-листы) и т.п. Помимо определения escape point может потребоваться анализ возможности возникновения подобной проблемы на других участках операционной деятельности и или в другой продукции.
Зная коренную причину и точку потери контроля, разрабатываются необходимые корректирующие действия – как для продукции, так и для системы качества. Важно, чтобы до начала их внедрения была достигнута уверенность, что предлагаемые корректирующие действия будут эффективны и не создадут других, вторичных проблем.
Последовательность выполнения этапа:
- Генерация предложений (решений), предлагаемых для устранения коренной причины проблемы качества.
- Выбор наилучшего алгоритма реализации решения и его обоснование.
- Согласование корректирующих действий для коренной причины.
- Согласование корректирующих действий для точки потери контроля (escape point).
D6 – Реализация и оценка достаточности корректирующих действий
На данном этапе внимание уделяется плану реализации (внедрения) корректирующих действий. Как раз здесь уместно вспомнить о цикле PDCA – планируй (Plan), делай (Do), контролируй (Check) и воздействуй (Act).
При планировании принимаются во внимание следующие факторы:
- Требуется четко определить ответственность и полномочия по внедрению корректирующих действий.
- Определить способы информационного взаимодействия всех вовлеченных в процесс внедрения должностных лиц и (или) структурных подразделений.
- Необходимость удержания под контролем предлагаемых изменений (многие корректирующие действия по своей природе являются изменениями, а значит требуют дополнительной оценки в системе контроля изменений).
Также важно определить:
- Методику оценки эффективности корректирующих действий (можно пойти по пути ответа на вопросы «Кто?», «Что?», «Где?» и «Как?»).
- Набор данных, которые нужно собирать для валидации корректирующих действий (в течение какого времени и в каком объеме).
- Основной лозунг данного этапа: «Если у нас нет наглядных доказательств решения проблемы – мы проблему не решили».
Форма, которая заполняется на данном этапе, может содержать:
- Подразделения и ответственные лица, вовлеченные в реализацию корректирующих действий.
- План по внедрению (ответственные, сроки, ресурсы).
- Анализ рисков при внедрении корректирующих действий.
- Параметры выполнения плана внедрения.
- Сроки отмены временных мер.
- Формат взаимодействия команды ответственных за внедрение корректирующих мероприятий.
- Форма предоставления данных для оценки достаточности корректирующих мероприятий (например, диаграмма Парето, контрольные карты, расчет индексов воспроизводимости процесса и т.п.).
- Программа оценки достаточности корректирующих действий (параметры для измерения долгосрочных результатов).
- Документация, подлежащая разработке и (или) актуализации.
и др.
D7 – Выбор предупреждающих действий
Главной задачей при разработке САРА является не только предупреждение повторного возникновения проблемы, но и определение мероприятий, применимых для схожих процессов для предотвращения схожих проблем. На этом этапе 8D проводится анализ целесообразности внесения исправлений и (или) изменений в производственную и (или) системную документацию:
- Планы управления рисками и (или) результаты ранее проведенного анализа рисков для качества.
- Блок-схемы процессов.
- Процедуры, инструкции или методики.
- Проверочные листы (чек-листы).
- Планы отбора образцов.
- Стратегия контроля.
и др.
Также на данном этапе уделяется внимание вопросам, поднятым на этапах D2 и D4, относящихся к системным ошибкам. Основная цель – определить, какие изменения необходимо внести в процесс или систему, допустившую (позволившую) реализоваться проблеме качества.
D8 – Закрытие проблемы
На данном этапе требуется собрать мнения участников команды 8D об эффективности методики для устранения конкретной проблемы качества. Как правило, для этого требуются ответы на вопросы:
- Методика 8D была эффективной для данной проблемы?
- Требуются ли какие-то изменения в методике 8D?
Если требуются, тогда составляется план улучшения процесса 8D и назначаются ответственные лица.
Заключение
Методика 8D не очень-то и отличается от других методик управления корректирующими и (или) предупреждающими действиями. Те же преимущества, те же недостатки. В то же время пример по структурированию процесса на 8 этапов представляется интересным и удобным для разъяснения персоналу, вовлекаемому в работу с САРА.
? Больше информации на Telegram-канале СЛУЖБА КАЧЕСТВА
Обсуждения, дискуссии вопросы-ответы ? в чате специалистов по качеству