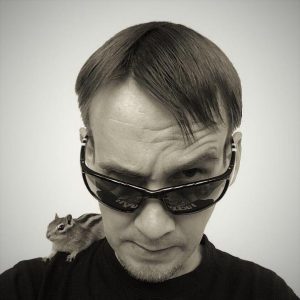
Константин Морозов, специалист по GMP, аудитор фармацевтических предприятий
Как отмечено во введении к меморандуму PIC/S PI 028-2 «GMP инспекция, связанная с упаковкой» (GMP inspection related to packaging) [1], процесс упаковки лекарственных средств входит в число факторов риска, которые могут повлиять на качество готовых лекарственных средств, а также могут привести к перепутыванию. Целью этого документа является предоставление руководства для GMP-инспекторов при подготовке к проверкам. Он направлен на определение минимальных требований, приемлемых для инспектора, а также требований, обеспечивающих максимальную безопасность готовой продукции («лучшие практики»). Данный документ может быть полезен и производителям лекарственных средств, но он содержит всего восемь страниц и поэтому не может подробно ответить на многие вопросы, связанные с упаковкой. В частности, он не дает ответы на ряд вопросов, которые могут возникнуть при рассмотрении раздела «Операции по упаковке» Главы 5 части I Правил надлежащей производственной практики (Good Manufacturing Practice, GMP). Некоторые требования к операциям по упаковке могут трактоваться по-разному, а производители стесняются задавать «неудобные» вопросы представителям инспектората или регулятора. В течение многих лет моя трудовая деятельность была связана с процессами упаковки, на которые мне удалось взглянуть с разных сторон — начальника участка упаковки, руководителя отдела обеспечения качества и специалиста по подготовке к GMP инспекциям. В этой статье я постараюсь ответить на некоторые вопросы, поделиться своей практикой и той практикой, которую мне удалось увидеть на разных производственных площадках в разных странах.
Перед началом рассмотрения требований к операциям по упаковке вспомним определение термина упаковка (packaging), который используются в Правилах GMP: «все операции, включая фасовку и маркировку, которые необходимо пройти нерасфасованной продукции, чтобы стать готовой продукцией». В данной статье мы не будем рассматривать наполнение стерильной продукции, которое, как правило, не следует рассматривать как часть процесса упаковки. Также мы не будем рассматривать такое понятие, как маркировка упаковок лекарственных препаратов средствами идентификации. Некоторые вопросы, касающиеся упаковки и маркировки, уже были затронуты мной несколько лет тому назад в статье «Анализ несоответствий, связанных с упаковкой, выявляемых при инспектировании» [2].
Как свести к минимуму риск перекрестной контаминации, перепутывания или подмены при составлении планов операций по упаковке? Какое физическое разделение предусматривается при упаковке продукции различных видов в непосредственной близости друг от друга?
Перекрестную контаминацию необходимо предотвращать, прежде всего за счет правильного проекта помещений и оборудования. Планировочные решения рабочих зон и внутрипроизводственных зон хранения должны обеспечивать последовательное и логичное размещение оборудования и материалов, сводящее к минимуму риск перепутывания различных лекарственных препаратов или их компонентов.
Например, участок упаковки твердых лекарственных форм разделяется на зоны первичной и вторичной упаковки. Упаковочные линии должны быть установлены таким образом, чтобы вход-выход персонала, работающего в этих различающихся зонах, осуществлялся раздельно, и чтобы поступление-возврат материалов, используемых в этих различающихся зонах, также осуществлялся раздельно.
В зоне первичной упаковки основное внимание уделяется защите продукта и поверхностей, с которыми он контактирует. Мониторинг окружающей среды и квалификация инженерных систем, используемых в этой зоне, имеют большое значение. Для предотвращения перекрестной контаминации каждую блистерную машину в этой зоне устанавливаются в отдельном помещении (полное физическое разделение).
В зоне вторичной упаковки картонажные машины и другие установки, входящие в состав линий, могут быть также установлены в отдельных помещениях. Однако это не очень удобно для работы, поэтому чаще всего эта зона представляет собой одно большое помещение, разделенное перегородками. Нет требования того, чтобы эти перегородки были высотой до самого потолка. Тем не менее перегородки должны быть настолько высокими и протяженными (до самого конца линии), чтобы предотвратить риск случайного перепутывания различной продукции или компонентов упаковки.
Как перед началом операций по упаковке убедиться в том, что рабочая зона, упаковочные линии и другое оборудование являются чистыми и не содержат любые использовавшиеся ранее лекарственные препараты, материалы или документы?
Для начала разберем понятие line clearance, которое используется в пункте 5.50 Правил GMP ЕС (EU GMP) [3]. Line clearance — это не просто очистка линии (line cleaning), которую следует проводить согласно соответствующей процедуре, это стандартизированная производственная процедура, обеспечивающая отсутствие на оборудовании и в рабочих зонах продукции, документов и материалов, оставшихся после предыдущего процесса.
Такая проверка должна быть оформлена документально в записях по производству серии, в журналах по использованию помещений и эксплуатации оборудования или отражена в другой системе документального оформления. Процедуры line clearance помогают операторам подготовиться к следующему запланированному процессу и избежать неправильной маркировки или перекрестной контаминации продукции. То есть это более комплексная процедура, чем очистка оборудования и уборка помещений.
На некоторых современных предприятиях line clearance уже претерпела значительную эволюцию. Исторически первым практикуемым методом было использование чек-листа одним оператором. Следующим и наиболее распространенным методом стало привлечение двух операторов, один из которых должен проводить независимую проверку. При последующем развитии этого метода оператор проверял линию, следуя порядковым номерам, которые указывали ему путь (специальные стикеры на оборудовании). А самый новый метод уже включал в себя следование оператора за нанесенной на полу линией со стикерами, указывающими количество конкретных точек для осмотра. Вполне возможно, что и этот метод проверки в дальнейшем может быть улучшен. Важно понимать, что стикеры, которые могут быть использованы для маркировки оборудования, не должны со временем отклеиться и сами стать источниками контаминации. Чек-листы и схемы, где указаны точки контроля, нужно периодически пересматривать и обновлять при необходимости.
Требуется ли указывать наименование и номер серии упаковываемой продукции на каждой установке, входящей в состав линии?
Если все установки, входящие в состав упаковочной линии, расположены в отдельном помещении или в выделенной перегородками части помещения, то обычно в каждой зоне упаковки достаточно одной этикетки (такой подход нужно описать в соответствующей процедуре). Таким образом можно соблюсти требование по маркировке этикетками всех используемых основных единиц оборудования.
Обычно этикетки размещаются при входе на двери помещения или непосредственно рядом с дверью, недалеко от идентификационной таблички (или на перегородке между линиями в зоне вторичной упаковки). Этикетки размещаются так, чтобы их было видно входящему в помещение сотруднику. Помимо наименования и номера серии на этикетке может быть указан код упаковываемой продукции (числовой или штриховой, в случае использования системы сканирования), а вся нанесенная на этикетку информация должна быть четкой и разборчивой. Некоторые производители используют для идентификации упаковочного места/линии этикетки такой же формы, как и те, которыми маркируются транспортные короба с готовой продукцией.
Каким образом при поступлении нерасфасованной продукции и упаковочных материалов на участок упаковки проверить их количество, идентичность и соответствие инструкциям по упаковке?
Иногда производители задаются вопросом, каким образом можно проверить количество тех или иных упаковочных материалов. С материалами блистерной упаковки, расход которых осуществляется в килограммах (такими как формовочная пленка, покрывающая алюминиевая фольга), проблем обычно не возникает — важно только учитывать вес втулки рулона.
Остаток картонных пачек во вскрытом транспортном коробе обычно пересчитывают вручную. В каждом коробе пачки должны быть уложены одинаково — с применением прокладок между слоями и рядами, что облегчает подсчет остатка и общую калькуляцию.
Если остаток инструкций по применению (листков-вкладышей) пересчитывать вручную поштучно, то на это уйдет много времени, а сложить их потом обратно ровной стопкой будет сложно — впоследствии могут возникнуть проблемы с их использованием на фальцевальном устройстве картонажной машины. Проверить их количество можно с использованием весов.
Узнать количество самоклеящихся этикеток в рулоне проще всего по номерам, отпечатанным на обратной стороне подложки, но на практике этикетки с индивидуальными номерами встречаются редко. Система подсчета этикеток типа reel-to-reel представляет собой автономную настольную установку, в которой используется предустановленный счетчик (существует и система пересчета этикеток, оснащенная ультразвуковым датчиком, что позволяет пересчитывать прозрачные и темные этикетки). Другие способы подсчета этикеток являются менее точными.
Важно понимать, что у производителей упаковочных материалов есть свои допустимые отклонения количества материалов в групповой и транспортной упаковке. Например, допустимое отклонение количества штук картонных пачек в транспортном коробе может составлять ±0,5% от заявленного на индивидуальном маркировочном ярлыке. Зачем нам нужно более точно определять количество нерасфасованной продукции и упаковочных материалов (как при их поступлении на участок упаковки, так и по окончанию процесса упаковки и при возврате остатков на склад)? — чтобы правильно составлять материальный баланс по продукции и упаковочным материалам.
Инструкции по упаковке должны среди прочего включать такие сведения (или ссылки на них), как полный перечень всех необходимых упаковочных материалов, включая их количества, размеры и типы с указанием кода или номера, относящихся к спецификациям на каждый упаковочный материал; образец или копию соответствующих печатных упаковочных материалов и образцы, указывающие на место нанесения номера серии и срока годности продукции.
Некоторые производители включают в состав инструкций по упаковке пустые шаблоны записей по упаковке серии. Перечень всех необходимых упаковочных материалов может быть представлен в приложении к инструкции по упаковке (его могут называть «ведомость материалов», bill of materials и т. п.).
Что касается образцов (копий) соответствующих печатных упаковочных материалов и образцов, указывающих на место нанесения данных о серии продукции, то в инструкции по упаковке на них может быть приведена только ссылка. Эти образцы должны быть в наличии, но они могут храниться отдельно, особенно если размер образцов не позволяет приложить их к инструкции (например, картонная пачка большого размера). Образцы должны быть соответствующим образом промаркированы (также они могут быть заламинированы) — во избежание их случайного попадания в общий поток упаковки.
В качестве системы визуального контроля компонентов упаковки в фармацевтической промышленности используется числовое кодирование этих компонентов. Код может быть нанесен на все упаковочные материалы, где его можно прочитать — на покрывающую алюминиевую фольгу с печатью, картонные пачки, инструкции по применению, самоклеящиеся этикетки и пр. На печатных материалах обычно указывают не только код, но и актуальный номер версии макета упаковочного материала.
Как обеспечить чистоту материалов первичной упаковки до начала операции наполнения?
Чистоту материалов первичной упаковки, используемых в фармацевтической промышленности, должны в первую очередь обеспечивать организации-изготовители этих материалов. Стандарт ISO 15378:2017 «Первичные упаковочные материалы для лекарственных средств. Особые требования по применению ИСО 9001:2015 с учетом надлежащей производственной практики (GMP)» (Primary packaging materials for medicinal products — Particular requirements for the application of ISO 9001:2015, with reference to good Good Manufacturing Practice (GMP)) [4] устанавливает требования к системе менеджмента качества, применимой к первичным упаковочным материалам для лекарственных средств. Этот документ содержит требования стандарта ISO 9001:2015 «Системы менеджмента качества — требования» (Quality management systems — Requirements) [5] и дополнительно частные требования к первичным упаковочным материалам, которые позаимствованы и соответствующим образом адаптированы из Правил GMP. Реализация организациями, которые изготавливают первичные упаковочные материалы, принципов GMP при производстве и контроле качества имеет чрезвычайно важное значение для обеспечения безопасности пациентов, получающих лекарственные препараты — из-за непосредственного контакта первичной упаковки с препаратом. В разделе Production and service provision стандарта ISO 15378:2017 говорится о том, что организация-изготовитель материалов первичной упаковки должна разработать, утвердить и соблюдать документированные требования к чистоте этих материалов и процедуры по предотвращению контаминации продукции и оборудования. Подобные требования есть не только в этом международном стандарте, но и в некоторых локальных руководствах — например, в разделе Clean manufacturing and contamination control management «Руководства по надлежащей производственной практике для упаковочных материалов для лекарственных средств» (Guidance of Good Manufacturing Practice for packaging materials for medicinal products) [6], которое было издано Китайской национальной ассоциацией фармацевтической упаковки.
На фармацевтическом предприятии уровень контроля упаковочных материалов должен быть пропорционален рискам, связанным с конкретными материалами, с учетом источника их происхождения, производственного процесса, сложности цепи поставок и конечного назначения материала. Первичные упаковочные материалы считаются критическими для обеспечения соответствия лекарственного средства установленным требованиям, они должны закупаться у одобренных поставщиков, проходящих аудит.
Следует оценить необходимость и частоту проведения контроля микробиологической чистоты этих материалов. При необходимости тара поступающих материалов должна быть очищена, наружная упаковка удалена, материалы могут быть переложены в специальную тару при их перемещении в зону первичной упаковки и т. п.
На участке упаковки нужно также уделять внимание тому, как упакованы поступающие со склада и возвращаемые на склад материалы (отсутствию повреждений тары и целостности упаковки). При временном хранении первичных упаковочных материалов на участке упаковки они должны быть защищены от любой возможной контаминации. Не случайно некоторые из несоответствий, выявляемых инспекторами, по-прежнему звучат так: «Не предоставлено обоснование исключения проведения контроля микробиологической чистоты первичных упаковочных материалов», «Первичная упаковка (алюминиевые баллоны, флаконы и крышки) при входном контроле не испытываются на микробиологическую чистоту», «Согласно спецификации на саше, не предусмотрена и не проводится проверка бионагрузки саше для первичной упаковки препарата» и т. п.
Если маркировка осуществляется не сразу после фасовки и укупорки, то какие меры необходимо принять для гарантии того, что не произойдет перепутывания или ошибочной маркировки?
Между наполнением первичных упаковок, их маркировкой и упаковкой по различным причинам может пройти определенный промежуток времени. Должны быть разработаны и документально оформлены процедуры, описывающие порядок хранения немаркированных контейнеров, обеспечивающие невозможность их перепутывания и надлежащие условия хранения.
Продукция без маркировки должна быть физически изолирована при хранении, маркировка на таре с этой продукцией должна быть четкой и однозначно воспринимаемой. При транспортировании (особенно на другой участок или другую площадку, где будет осуществляться маркировка и упаковка) тару следует опломбировать таким образом, чтобы в случае нарушения или отсутствия пломбы получатель мог обратить внимание на возможность изменения содержимого. Материальный баланс по этой продукции должен рассчитываться особенно скрупулезно.
На линии для упаковки ампул, флаконов или предварительно наполненных шприцев может быть установлена система типа ring code inspection с высокой разрешающей способностью для проверки цветовых кодов, нанесенных на немаркированную продукцию. Такая система способна различать цвет колец на ампулах или цвет крышек флаконов. Если проверка цвета колец и крышек выполняется операторами, следует регулярно проверять цветовое зрение операторов, выполняющих визуальный контроль.
Каким образом нужно контролировать и документально оформлять правильность выполнения печатных операций, осуществляемых либо как отдельная технологическая операция, либо в процессе упаковки?
Согласно параграфу Materials examination and usage criteria части 211 Раздела 21 Свода федеральных нормативных актов США (Title 21 of the Code of Federal Regulations (CFR), Part 211) [7], печатающие устройства на производственных линиях (или связанные с ними), которые используются для нанесения маркировки на этикетки или пачки лекарственного препарата, должны контролироваться, чтобы гарантировать, что все печатные данные соответствуют печатным данным, указанной в записи по производству серии.
Как уже упоминалось, инструкции по упаковке должны среди прочего включать образцы, указывающие на место нанесения номера серии и срока годности продукции. В некоторых случаях, эти образцы показывают не только место нанесения данных о серии продукта, но и пример нанесения этих данных, например метод нанесения (печать, тиснение, печать с тиснением и др.), размер символов, расстояние между символами и т. п. Частота выполнения контроля работы печатающих устройств и печатных операций может быть разной, особенно в случае ручной маркировки, которую следует регулярно перепроверять (в начале упаковки/маркировки новой серии продукта, в начале смены, с регулярными интервалами и т. д.). Проверяется не только соответствие нанесенных данных тем данным, которые указаны в записи по упаковке серии, но и их читаемость и однозначность восприятия.
Если печатающее устройство на линии или отдельно стоящей установке предполагает использование наборных штампов для тиснения, необходимо уделять особое внимание обращению и хранению насадок-оттисков.
Записи по упаковке серии должны среди прочего содержать образцы использованного печатного упаковочного материала, включая образцы, с нанесенными номером серии, сроком годности и прочими дополнительными маркировочными данными. Если упаковка/маркировка проводится с перерывами, например в течение нескольких дней, то к записи должны быть приложены образцы упаковочного материала (в частности, пустые блистеры, картонные пачки, этикетки с нанесенными данными о серии продукта и т. п.), отобранные в каждый день выполнения производственных операций.
Какие меры нужно соблюдать для предотвращения перепутывания печатного материала?
Особое внимание следует уделять печатным материалам. Для этих материалов требование хранить в безопасных условиях, исключающих доступ посторонних лиц относится не только к складу, но и к участку упаковки. Безопасные условия хранения печатных материалов могут быть обеспечены различными способами, такими как использование отдельного помещения для их хранения, выделение закрывающейся на ключ зоны или использование закрывающихся на ключ шкафов для хранения печатных материалов в общей зоне хранения.
На одном поддоне нельзя хранить печатные материалы для разных видов продукции. Что касается хранения на одном поддоне разных партий печатного материала для одного вида продукции (например, при хранении очень небольших количеств), то есть такая практика: на поддон устанавливают высокие перегородки, которые физически полностью разделяют партии и предотвращают их перепутывание. Каждый «отсек» такого поддона должен быть промаркирован индивидуальной этикеткой и для каждой партии должен вестись индивидуальный учет. Еще эффективнее проблему хранения и учета небольших количеств/возвращаемых остатков материалов решают автоматизированные лифтовые стеллажи.
Разрешение на использование упаковочных материалов должно выдаваться только специально назначенными лицами в соответствии с утвержденной и документально оформленной процедурой.
Разрезанные этикетки и другие разрозненные печатные материалы должны храниться и транспортироваться раздельно в закрытой таре, исключающей их перепутывание.
Такое же требование относится, например, к картонным пачкам с нанесенными на них данными о серии продукта (если данные наносятся вне линии упаковки). Используемая для их хранения и транспортирования тара должна быть, в свою очередь, четко промаркирована. Перемещение этих материалов на упаковочную линию должно контролироваться и регистрироваться.
Разрезанные этикетки сейчас используются достаточно редко; это этикетки, которые «вырезаны» из листа или рулона с этикетками. Такие этикетки могут использоваться, например, для маркировки картонных коробок, содержащих несколько флаконов с вакциной для лечебно-профилактических учреждений. Согласно уже упоминавшемуся параграфу Materials examination and usage criteria части 211 Раздела 21 Свода федеральных нормативных актов США, при использовании разрезанных этикеток операции упаковки и маркировки должны включать одну из следующих специальных процедур контроля:
- Выделение линий для маркировки и упаковки каждой отдельной дозировки каждого отдельного продукта
- Использование соответствующего электронного или электромеханического оборудования для проведения 100%-ой проверки правильности маркировки во время выполнения операций или после их завершения; или же
- Использование визуального контроля для проведения 100%-ой проверки правильности маркировки во время выполнения операций по ручной маркировке или после их завершения. Такая проверка должна проводиться одним лицом и независимо проверяться вторым лицом
- Использование любого автоматизированного метода, включая разграничение по размеру и форме этикетки, который физически предотвращает неправильную маркировку с помощью оборудования для маркировки и упаковки.
В том же параграфе требований США упоминаются этикетки с «групповой печатью» (gang-printed). Такие этикетки встречаются еще реже; они представляют собой несколько этикеток для различных продуктов или дозировок, нанесенных на один лист-подложку. Требования США запрещают использование таких этикеток, если только они не отличаются друг от друга по размеру, форме и цвету достаточно сильно (но даже в последнем случае риск перепутывания этикеток остается высоким).
Контроль этикеток является примером ситуации применения процесса управления рисками для качества в области упаковки и маркировки: для планирования процедур контроля этикеток, учитывая возможность перепутывания этикеток разной продукции, в том числе разных версий одной и той же этикетки.
Про требования к печатным материалам и аудит поставщиков печатных вторичных упаковочных материалов можно прочитать здесь: Аудит поставщиков печатных вторичных упаковочных материалов
Какие проверки необходимо проводить на упаковочной линии для гарантии того, что все электронные устройства считывания кода, счетчики этикеток и аналогичные устройства работают правильно?
Современные высокоскоростные упаковочные линии включают в себя оборудование, оснащенное большим числом механических, оптических и электрических контрольных устройств, передающих визуальные и/или звуковые сигналы. Элементами технических систем, предназначенных для измерения, сигнализации, регулирования и управления этими устройствами, являются датчики.
Проверки правильности работы электронных устройств/датчиков должны проводиться в начале процесса упаковки, а затем с определенными интервалами. Обычно эти проверки проводятся операторами, а дополнительный контроль выполняется персоналом подразделения контроля качества. Например, на линии упаковки твердых лекарственных форм проверке могут подлежать: датчик обнаружения микротрещин в пленке холодного формования, датчик обнаружения места склейки формовочной пленки, датчик обнаружения места склейки покрывающей алюминиевой фольги, устройство контроля наличия продукта в блистере (камера), датчик наличия инструкции в картонной пачке, весовой датчик (конвейерные весы) и т. п.
В качестве примера можно разобрать два вида тестирования — проверку корректной работы датчиков считывания фармакода и контроль герметичности блистерной упаковки (второй вид проверки не связан с каким-то одним датчиком, это комплексная проверка работы одного из узлов блистерной машины).
Фармакод (pharmacode, pharmaceutical binary code) является стандартом штрихового кода, используемый в фармацевтической промышленности в качестве системы автоматизированного контроля компонентов упаковки. Фармакод может быть нанесен на все упаковочные материалы, с которых он читается датчиком на оборудовании — на покрывающую алюминиевую фольгу с печатью, картонные пачки, инструкции по применению, самоклеящиеся этикетки и пр.
Проверка корректной работы датчиков считывания фармакода важна для гарантии правильности работы устройств и предотвращения перепутывания компонентов упаковки. Для этого на тестируемых образцах модифицируют имеющийся фармакод, например черным маркером добавляют дополнительный штрих на белом пространстве между отдельными штрихами. Если датчик считывания фармакода работает правильно, тестируемые образцы будут отбракованы, оборудование остановится/выдаст сообщение о некорректном фармакоде (в зависимости от его настроек). Частота выполнения проверки датчиков считывания фармакода может быть, например, такой:
- в начале упаковки новой серии продукта;
- в начале смены;
- при смене номера партии упаковочного материала, на который нанесен фармакод;
- в случае длительного простоя оборудования (например, более 30 минут);
- после устранения неисправности, изменения настроек датчика считывания фармакода;
- после отключения электричества;
- в случае возникновения повторяющейся ошибки, о которой сигнализирует оборудование.
В ОФС.1.1.0025.18 «Упаковка, маркировка и транспортирование лекарственных средств» [8] приведено следующее определение контурной ячейковой упаковки (блистера): «гибкая упаковка из комбинированных материалов, состоящая из двух слоев, один из которых представляет собой ТЕРМОФОРМОВАННЫЕ ячейки, повторяющие форму упаковываемого лекарственного препарата; лекарственное средство из упаковки извлекается путем выдавливания или вскрытия». При этом кроме термоформования ячейки блистера могут быть получены и методом ХОЛОДНОГО формования. В «Требованиях к маркировке лекарственных средств для медицинского применения и ветеринарных лекарственных средств», утвержденных Решением Совета ЕЭК от 03.11.2016 г. № 76 [9], приведено несколько отличающееся определение блистера: «гибкая упаковка с лекарственным средством (ветеринарным средством) в отформованных ячейках, из которых лекарственное средство (ветеринарное средство) извлекается путем ВЫДАВЛИВАНИЯ». При этом кроме обычных блистеров типа push-through сейчас встречаются и блистеры типа child resistant and senior friendly с более сложной системой извлечения продукта (вскрытие + выдавливание).
При использовании метода термоформования на блистерной машине пластиковая пленка сначала проходит через узел предварительного нагрева, в результате чего пластик размягчается и становится гибким; затем теплый пластик поступает на узел формовки, где под большим давлением (от 4 до 8 бар) формуются блистерные ячейки; форма охлаждается, так что пластик снова становится жестким и сохраняет свою форму при извлечении из формы. При использовании метода холодного формования пленка ламината на основе алюминия просто запрессовывается в форму с помощью штампа. На узле термосварки пленка с отформованными и заполненными продуктом ячейками соединяется с покрывающей алюминиевой фольгой под давлением и нагреванием. Стандартный цикл нагрева при сварке занимает несколько секунд (например, при сварке роликами, при скорости блистерной машины до 200 блистеров/мин, средняя температура может быть 250°С).
Контроль герметичности блистерной упаковки важен для обеспечения сохранности лекарственных средств. Герметичная упаковка — это первичная упаковка, конструкция которой самостоятельно или в комплекте с укупорочным средством обеспечивает непроницаемость газов, паров и жидкостей при обычных условиях хранения, транспортирования и реализации. Чаще всего для тестирования блистеров на герметичность проводится вакуум тест (leak test, blue dye test) с использованием раствор индикатора — метиленового синего. Тестер герметичности блистерной упаковки состоит из электронного блока управления, встроенного вакуумного насоса и вакуум-эксикатора — герметично закрывающегося сосуда, соединенного с вакуумным насосом. Подготовленные образцы блистеров полностью погружают в заполненный раствором красителя эксикатор, при необходимости накрывают сверху удерживающей пластиной с отверстиями, эксикатор закрывают крышкой. Тестер с помощью вакуумного насоса создает разрежение в 400-600 мбар, после чего вакуумный насос останавливается и давление сбрасывается до атмосферного. Образцы достают из эксикатора, обмывают водой, вытирают салфеткой и оценивают визуально (в случае непрозрачной формовочной пленки продукт извлекается из блистера). При обнаружении окрашенной жидкости внутри образца блистера образец считается негерметичным. Частота выполнения контроля герметичности блистеров с твердыми лекарственными формами может быть, например, такой:
- в начале упаковки новой серии продукта;
- в начале смены;
- при смене номера партии формовочной пленки и покрывающей алюминиевой фольги;
- в случае длительного простоя оборудования (например, более 30 минут);
- после устранения неисправности или ремонта узла термосварки;
- в случае изменения температуры термосварки и скорости работы блистерной машины;
- после отключения электричества;
- с регулярными интервалами (например, не реже чем один раз в два часа при использовании метода термоформования блистерных ячеек или раз в час при использовании метода холодного формования).
К сожалению, контроль герметичности блистеров с раствором красителя — это не только разрушающий метод, но и субъективный, поскольку он в значительной степени зависит от суждения оператора. Сегодня передовыми методами проверки являются неразрушающие методы, обеспечивающие большую точность, поскольку они могут идентифицировать отверстия размером до 5 мкм (например, с использованием устройства типа BlisterScan, где технологии 3D сочетаются с перепадом давления и вакуумом).
Ниже приведен ряд советов одного из производителей блистерных машин [10], которые необходимо учитывать в качестве стандартной процедуры при упаковке таблеток и капсул для достижения лучшей герметичности блистерной упаковки:
- уточняйте тип упаковочного материала для продукта (большинство ошибок, возникающих при формовании и сварке, возникают из-за неправильной температуры и давления);
- приобретите соответствующие части для сварки (при кажущейся отличной герметизации при сварке остаются крошечные пространства, известные как микроканалы);
- поддерживайте хороший узор сетчатой накатки (когда узор накатки от роликов или плит не соответствует давлению машины, сварка становится неравномерной);
- ухаживайте за частями узла сварки (большое количество глубоко въевшейся грязи и остатков материалов может осаждаться на частях для сварки).
Каковы требования к маркировке упаковочных материалов, наносимой при упаковке?
В «Требованиях к маркировке лекарственных средств для медицинского применения и ветеринарных лекарственных средств», утвержденных Решением Совета ЕЭК от 03.11.2016 г. № 76, приведено следующее определение маркировки: «информация, нанесенная на упаковку лекарственного средства (ветеринарного средства)».
Маркировка лекарственных средств (ветеринарных средств) должна быть легко читаемой, удобочитаемой, понятной и достоверной и не вводить в заблуждение потребителей (приобретателей) лекарственного препарата и ветеринарного лекарственного препарата.
Пункт 5.58 Правил GMP ЕС относится не к маркировке в целом, а к информации, нанесенной с помощью печати или методом тиснения, то есть к данным о серии, для которых отчетливость и устойчивость к выцветанию и стиранию имеет большое значение.
К сожалению, при переводе пункта 64. в Приложении 2 к Правилам GMP ЕС [11] слово labels было также переведено как маркировка, хотя требование подтверждения устойчивости в случае использования сверхнизких температур хранения относится не к маркировке в целом, а к этикеткам. Такое требование может относиться, например, к ампулам с вакциной, хранящимся в сосудах Дьюара в замороженном виде (здесь compatibility подразумевает устойчивость самих этикеток, которые не должны отклеиваться от ампул). Подтвердить устойчивость этикеток можно с помощью валидационных испытаний. Можно также воспользоваться архивными образцами, которые хранят в целях подтверждения идентичности: условия их хранения должны соответствовать требованиям, установленным при регистрации лекарственного средства (например, хранение при пониженной температуре, если требуется).
Можно ли возвращать на упаковочную линию взятые с нее образцы?
Авторы статьи «Аналитический обзор ошибок русскоязычной версии Правил GMP ЕС» [12] когда-то писали, что фразу Samples taken away from the packaging line should not be returned в пункте 5.59 Правил GMP ЕС правильнее перевести «Образцы, ВЫНЕСЕННЫЕ ЗА ПРЕДЕЛЫ упаковочной линии, не следует возвращать обратно». Некоторые инспектора действительно трактуют этот пункт таким образом, что после того, как образец продукции попадает в руки оператора на упаковочной линии, то он не может быть возвращен обратно на линию.
Образцы, взятые на линии для неразрушающего контроля, не следует возвращать в общий поток упаковки как вздумается. Отдельные компоненты упаковки (например, взятые оператором для визуального контроля непосредственно в зоне упаковки) могут быть возвращены на линию — после их дополнительной проверки, и только в определенных и обозначенных стикерами на оборудовании местах. Например, блистеры могут быть возвращены в общий поток упаковки через магазин ручной подачи блистеров на картонажной машине, а комплектные упаковки могут быть возвращены перед конвейерными весами. Учет количества возвращаемых образцов является очень важным при расчете выхода и составлении материального баланса. Чтобы предотвратить риск случайного перепутывания, такие действия должны выполняться под контролем, а последовательность их выполнения должна быть четко описана в соответствующей процедуре.
При каких условиях возможен возврат упакованной продукции в производство?
Как правило, этот вопрос связан с операциями повторной упаковки (замена материалов вторичной упаковки) или повторной расфасовки (замена материалов первичной упаковки). Это один из самых щепетильных вопросов по упаковке, ответ на который можно найти не только в пункте 5.60, но и в пункте 5.68 Правил GMP, посвященном повторному использованию (в данном случае — всей серии). Общие условия для возврата упакованной продукции в производство — для повторной упаковки/расфасовки серии:
- при упаковке продукции возникли непредвиденные обстоятельства;
- было проведено расследование;
- была выполнена специальная проверка и учтены возникающие риски, включая любое возможное влияние на срок годности;
- было получено разрешение лица, имеющего соответствующие полномочия, и санкционирование было сделано заранее;
- был оформлен протокол вышеприведенных действий;
- деятельность по повторному использованию серии была осуществлена в соответствии с установленной процедурой и документально оформлена.
Следует помнить, что в некоторых случаях в программу текущего испытания стабильности
следует включать дополнительные серии, в частности после любого значительного отклонения в процессе упаковывания.
Только при надлежащем выполнении всех этих условий возврат упакованной продукции в производство не окажет влияния на качество, эффективность, безопасность, подлинность и чистоту лекарственного препарата, и не приведет к серьезным проблемам во время GMP-инспектирования.
Как правило, сама процедура повторной упаковки не вызывает у производителей слишком много вопросов. Например, при замене в потребительских упаковках инструкций по применению, операции по пересмотру продукции и повторной упаковке могут осуществляться с учетом таких предписаний: осторожно вскрывать транспортные короба, не повреждая содержимое; аккуратно вскрывать потребительские упаковки, не повреждая клапаны картонных пачек и блистеры; извлеченные из потребительских упаковок блистеры собирать в промаркированные контейнеры; выполнять действия по устранению инструкций, несоответствующих по показателям качества, согласно протоколу переупаковки; осуществлять замену устраненных инструкций соответствующими по показателям качества инструкциями и т. д.
Процедура повторной расфасовки вызывает намного больше вопросов. Например, для твердых лекарственных форм первый же вопрос связан с извлечением таблеток или капсул из блистеров. Для того, чтобы этот процесс не приводил к повреждению продукции и ее контаминации, используются деблистерные машины; такие установки могут быть ручными или автоматизированными. Необходимо проводить квалификацию и валидацию очистки этого вида производственного оборудования.
В том случае, когда повторной расфасовке подлежит не вся серия, а только ее часть, необходимо осуществлять возврат извлеченной из блистеров продукции только в самом конце упаковки серии. Как правило, возможен только один цикл повторной расфасовки в блистеры, так как сложно доказать, что многократная расфасовка не окажет какого-либо негативного влияния на готовую продукцию. Речь здесь идет как о большем риске контаминации продукции, так и о рисках механического повреждения при неоднократном извлечении из блистеров, а также о возможном негативном влиянии высокой температуры (как уже упоминалось, средняя температура на узле термосварки может быть 250°С, хотя нагрев занимает только несколько секунд). В записи по упаковке серии необходимо регистрировать номера транспортных коробов с повторно расфасованной продукцией и проводить испытания на микробиологическую чистоту с использованием образцов продукции, отобранных из этих коробов.
Что может не являться существенным или необычным расхождением, которое может быть установлено во время составления баланса между количеством нерасфасованной продукции, печатного упаковочного материала и числом произведенных единиц готовой продукции?
Следует применять процедуры сопоставления количества выданных, использованных и возвращенных упаковочных материалов и нерасфасованной продукции, чтобы можно было оценить расхождения с числом произведенных единиц готовой продукции (составить материальный баланс). Факты расхождения необходимо расследовать с установлением причины этого расхождения до выдачи разрешения на выпуск.
Как уже отмечалось, у производителей упаковочных материалов есть свои допустимые отклонения количества материалов в групповой и транспортной упаковке, поэтому на практике встречаются случаи излишних количеств материалов, которые не были обнаружены при приемке. Это обстоятельство нужно также учитывать при обосновании того, является ли установленное во время составления баланса расхождение существенным/необычным или оно укладывается в допустимые пределы, установленные производителем. Как правило, недорасход упаковочных материалов/значительные их остатки должны вызывать больше вопросов. Например, в случае большого числа оставшихся после упаковки серии инструкций, при расследовании необходимо среди прочего убедиться в том, что в процессе упаковки проводились все проверки правильности работы датчика наличия инструкции в картонной пачке и конвейерных весов.
Что касается расчета и проверки выхода готовой продукции, то в некоторых случаях выход продукции, превышающий 100%, является объяснимым. Например, это возможно при расфасовке таблеток, когда учет количества нерасфасованной продукции осуществляется в килограммах, а для расчета планируемого выхода готовой продукции используется средняя масса одной таблетки. Допустимые пределы выхода должны быть установлены производителем с учетом таких обстоятельств.
Как нужно поступать с упаковочными материалами, оставшимися после завершения операций по упаковке?
Утвержденная процедура возврата на склад немаркированных упаковочных материалов должна включать в себя двойной контроль: сотрудники участка упаковки проверяют количество возвращаемых материалов (как при составлении материального баланса по каждой серии, так и при сдаче остатков на склад); сотрудники склада также проверяют количество этих материалов. Возвращенные материалы следует содержать и хранить таким образом, чтобы предотвратить перепутывание и обеспечить надлежащую идентификацию.
Оставшиеся упаковочные материалы с нанесенными на них данными о серии должны быть уничтожены с последующим документальным оформлением, и они могут быть приведены в негодность еще на участке упаковки, что является предпочтительным (например, некоторые материалы из бумаги и картона могут быть надорваны или надрезаны; этикетки, нанесенные на флаконы, могут быть перечеркнуты маркером; продукт из блистеров может быть извлечен вручную или с помощью деблистерных машин и т. п.).
Многие производители передают деятельность по уничтожению производственных отходов на аутсорсинг. При этом нужно учитывать, какие виды отходов и в каком виде передаются на уничтожение. Особый риск могут представлять отходы печатных упаковочных материалов, которые предварительно не были приведены в негодность — изготовители поддельных лекарственных средств могут не только копировать оригинальную продукцию, но и повторно использовать неутилизированные отходы. Производитель должен контролировать уничтожение этих материалов. Эффективной мерой является видеозапись процесса уничтожения. Перед заключением договора на утилизацию производитель должен провести аудит организации, которая будет осуществлять эту деятельность, чтобы подтвердить, что организация соответствует предъявляемым требованиям, в том числе по безопасности.
Кроме защиты от фальсификации, необходимо подумать и о защите окружающей среды, которая становится все более важной во многих странах. Как написано в Приложении 9 к TRS 902 ВОЗ «Руководство по упаковке фармацевтической продукции» (Guidelines on packaging for pharmaceutical products) [13], фармацевтическая упаковка представляет собой очень небольшой процент отходов, но ее утилизация может создать проблемы для окружающей среды. Должны быть приняты меры для надлежащего и безопасного хранения отходов, ожидающих утилизации.
В заключение хотелось бы привести ряд важных контрольных вопросов из меморандума PIC/S PI 028-2, в котором описаны различные области, которые могут быть оценены в ходе GMP-инспекции процессов упаковки и маркировки. Производители лекарственных средств могут включить эти вопросы в свой вопросник, использующийся при проведении самоинспекции на участке упаковки.
Область | Важные вопросы |
Качество и закупки упаковочных материалов |
|
Получение
упаковочных материалов |
|
Складские зоны
|
|
Контроль качества
|
|
Производственные помещения (зона упаковки)
|
|
Упаковочное оборудование и процесс
|
|
Документация
|
|
Персонал
|
|
Обеспечение качества
|
|
Если в этой статье Вы не нашли ответ на какой-то специфический вопрос, связанный с операциями по упаковке, то Вы можете задать его мне в чатах, посвященных GMP, производству и качеству лекарственных средств — я постараюсь найти ответ. Интерпретируют ли фармацевтические инспектора требования к операциям по упаковке таким же образом, как и я, одобрят ли они все описанные мной практики? — не уверен. В любом случае, сегодня инспектора оценивают соответствие производства лекарственных средств и ФСК производителя с применением риск-ориентированного подхода. Управление рисками для качества является частью деятельности уполномоченных органов, в том числе для оценки значимости данных, полученных при инспектировании. При анализе несоответствий каждая ситуация рассматривается с учетом таких факторов, как безопасность для пациента, качество, доступность и цена лекарственного препарата.
Представленный материал подготовлен с использованием данных, актуальных на 23.06.2023. В случае получения новых или дополнительных данных статья может быть обновлена.
Константин Морозов
ССЫЛКИ:
- Pharmaceutical Inspection Co-operation Scheme / PIC/S GMP Inspection Related to Packaging (PI 028-2). URL: https://picscheme.org/docview/3822 (дата обращения 06.2023)
- TechnoPharma / Анализ несоответствий, связанных с упаковкой, выявляемых при инспектировании. URL: https://technopharma.ru/analiz-nesootvetstvij-svyazannyh-s-upakovkoj-vyyavlyaemyh-pri-inspektirovanii/ (дата обращения 23.06.2023)
- The rules governing medicinal products in the European Union — Volume 4 — EU Guidelines for Good Manufacturing Practice for Medicinal Products for Human and Veterinary Use / Chapter 5 — Production. URL: https://health.ec.europa.eu/system/files/2016-11/chapter_5_0.pdf (дата обращения 23.06.2023)
- ISO / ISO 15378:2017 Primary packaging materials for medicinal products — Particular requirements for the application of ISO 9001:2015, with reference to good manufacturing practice (GMP). URL: https://www.iso.org/standard/70729.html (дата обращения 23.06.2023)
- ISO / ISO 9001:2015 Quality management systems — Requirements. URL: https://www.iso.org/standard/62085.html (дата обращения 23.06.2023)
- CNPPA / Guidance of Good Manufacturing Practice for Packaging Materials for Medicinal Products. URL: https://cnppa.org/Public/editor/attached/file/20200426/20200426131838_43156.pdf (дата обращения 23.06.2023)
- FDA / Title 21 of the Code of Federal Regulations (CFR) / Part 211 / Subpart G — Packaging and Labeling Control / Materials examination and usage criteria. URL: https://www.accessdata.fda.gov/scripts/cdrh/cfdocs/cfcfr/CFRSearch.cfm?fr=211.122 (дата обращения 23.06.2023)
- Электронный фонд правовых и нормативно-технических документов / ОФС.1.1.0025.18 Упаковка, маркировка и транспортирование лекарственных средств. URL: https://docs.cntd.ru/document/573913018 (дата обращения 23.06.2023)
- Евразийский экономический союз / Решение Совета Евразийской экономической комиссии от 03 11.2016 г. № 76 «Об утверждении Требований к маркировке лекарственных средств для медицинского применения и ветеринарных лекарственных средств». URL: https://docs.eaeunion.org/docs/ru-ru/01411918/cncd_21112016_76 (дата обращения 23.06.2023)
- Accupack Engineering / Post / Tips for Smooth Blistering Sessions. URL: https://www.accupackengineering.com/post/tips-for-smooth-blistering-sessions/ (дата обращения 23.06.2023)
- The rules governing medicinal products in the European Union — Volume 4 — EU Guidelines for Good Manufacturing Practice for Medicinal Products for Human and Veterinary Use / Annex 2 — Manufacture of Biological active substances and Medicinal Products for Human. URL: https://health.ec.europa.eu/system/files/2019-02/2018_annex2_enpdf (дата обращения 23.06.2023)
- Сlimatecontrolsolutions / Новости партнеров / Аналитический обзор ошибок русскоязычной версии Правил GMP ЕС. URL: https://climatecontrolsolutions.ru/novosti-partnjorov/107-analiticheskij-obzor-oshibok-russkoyazychnoj-versii-pravil-gmp-es.html (дата обращения 23.06.2023)
- WHO / Publications / Overview/ TRS 902 — Annex 9: Guidelines on packaging for pharmaceutical products. URL: https://cdn.who.int/media/docs/default-source/medicines/norms-and-standards/guidelines/regulatory-standards/trs902-annexpdf?sfvrsn=82b4c57d_2&download=true (дата обращения 23.06.2023)